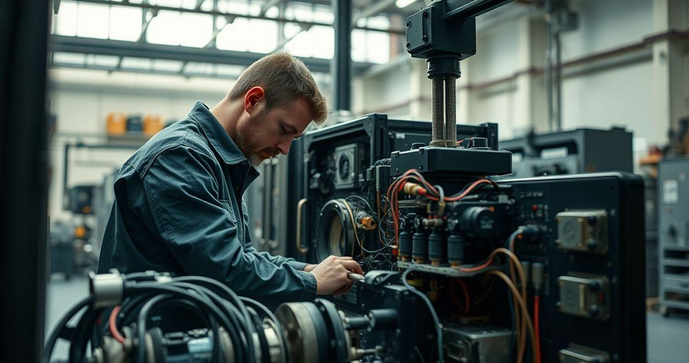
Importância da Manutenção Eletrônica Industrial
A manutenção eletrônica industrial desempenha um papel fundamental na operação eficiente das fábricas e indústrias. Ela se refere à preservação e ao reparo dos sistemas eletrônicos usados para controlar e monitorar equipamentos e processos. A falha em manter esses sistemas pode resultar em paradas inesperadas, perda de produtividade e aumento dos custos operacionais.
Um dos principais benefícios da manutenção eletrônica é a prevenção de falhas. Ao realizar manutenções regulares, as empresas podem identificar problemas antes que eles se tornem críticos. Isso não apenas reduz o tempo de inatividade, mas também aumenta a vida útil dos equipamentos, economizando recursos a longo prazo.
Adicionalmente, a manutenção eletrônica contribui para a eficiência energética. Sistemas em bom estado operam de maneira mais eficaz, consumindo menos energia e, consequentemente, reduzindo os custos com eletricidade. Além disso, ambientes bem mantidos são mais seguros, minimizando o risco de acidentes e aumentando a segurança dos trabalhadores.
A importância da manutenção eletrônica também se reflete nos resultados financeiros da empresa. Com a confiabilidade dos equipamentos, a produção se torna mais estável e previsível, permitindo uma melhor programação e planejamento de recursos. Isso se traduz em uma vantagem competitiva no mercado, comprovando que a manutenção não é apenas um custo, mas um investimento estratégico.
Por último, é importante destacar que a manutenção eletrônica deve ser realizada por profissionais qualificados. A complexidade dos sistemas eletrônicos requer conhecimentos específicos, e uma equipe bem treinada pode proporcionar uma gestão mais eficaz da manutenção, garantindo que todos os processos estejam alinhados com as melhores práticas do setor.
Principais Tipos de Manutenção Eletrônica
Os principais tipos de manutenção eletrônica são essenciais para garantir o funcionamento adequado dos equipamentos nas indústrias. Cada abordagem tem suas particularidades e é aplicada em diferentes situações. Vamos explorar os três tipos mais comuns de manutenção eletrônica:
1. Manutenção Preventiva: Este tipo de manutenção é programada e realizada regularmente para evitar falhas nos sistemas eletrônicos antes que elas ocorram. Geralmente, envolve inspeções, ajustes, limpezas e substituições de peças em intervalos pré-determinados. A manutenção preventiva ajuda a prolongar a vida útil dos equipamentos e a garantir uma operação contínua e eficiente.
2. Manutenção Corretiva: A manutenção corretiva é executada após a ocorrência de falhas. Seu objetivo é restaurar o funcionamento do sistema ou equipamento afetado. Esse tipo de manutenção pode ser planejada ou emergencial. Ao contrário da manutenção preventiva, que busca evitar problemas, a manutenção corretiva lida com as consequências das falhas, demandando tempo e recursos que poderiam ser evitados com a manutenção preventiva adequada.
3. Manutenção Preditiva: A manutenção preditiva utiliza tecnologias avançadas, como monitoramento em tempo real e análises de dados, para prever falhas antes que elas aconteçam. Ela analisa informações coletadas de sensores e sistemas de controle para identificar padrões que possam indicar desgaste ou problemas iminentes. Esta abordagem permite intervenções mais precisas e programadas, otimizando o uso de recursos e o tempo de inatividade.
Cada um desses tipos de manutenção tem um papel importante dentro da estratégia de gestão de ativos da indústria. A escolha do tipo apropriado depende das características do equipamento, dos requisitos de operação e da análise de custos e benefícios. Uma combinação eficaz desses métodos pode levar a uma melhoria significativa na eficiência operacional e na redução de custos.
Impacto da Manutenção na Produtividade
A manutenção eletrônica tem um impacto direto e significativo na produtividade das operações industriais. A forma como os equipamentos são mantidos pode determinar a capacidade de produção de uma fábrica e influenciar a eficiência geral dos processos.
1. Redução do Tempo de Inatividade: Equipamentos bem mantidos geralmente apresentam menos falhas e, portanto, menos paradas inesperadas. Isso significa que as linhas de produção podem operar de forma contínua, aumentando a capacidade produtiva. Menos tempo de inatividade se traduz em maior quantidade de produtos fabricados, impactando positivamente nos resultados financeiros da empresa.
2. Otimização do Desempenho Operacional: A manutenção regular não só evita que máquinas quebrem, mas também garante que elas operem em níveis ótimos de eficiência. Sistemas eletrônicos que funcionam adequadamente são capazes de produzir mais com menos recursos, como energia e matéria-prima, resultando em processos mais sustentáveis e econômicos.
3. Melhoria na Qualidade do Produto: Equipamentos em boas condições têm maior precisão e controle de qualidade em sua operação. Isso reduz a probabilidade de erros e desperdícios, garantindo que os produtos finais atendam aos padrões exigidos. A qualidade consistente dos produtos fortalece a reputação da empresa no mercado e aumenta a satisfação do cliente.
4. Aumento da Moral dos Funcionários: Um ambiente de trabalho onde as máquinas funcionam eficientemente aumenta a moral e a motivação dos funcionários. Eles podem realizar suas tarefas com mais confiança, sabendo que os equipamentos não os deixarão na mão. Isso cria um efeito positivo no ambiente de trabalho e contribui para uma cultura de melhoria contínua.
5. Planejamento e Agilidade: A manutenção adequada permite um melhor planejamento das atividades operacionais. Com sistemas de manutenção preditiva, as empresas podem antecipar e programar paradas para manutenção, minimizando o impacto na produção. A agilidade no reparo e na preparação para manutenções evita interrupções longas e socorros emergenciais que afetam diretamente a produtividade.
Em resumo, a relação entre manutenção eletrônica e produtividade é clara. Investir em uma abordagem de manutenção eficaz é crucial para qualquer operação industrial que vise maximizar sua eficiência, reduzir custos e permanecer competitiva no mercado global.
Técnicas para Realizar Manutenção Eficiente
Realizar uma manutenção eletrônica eficiente é crucial para garantir a operação contínua e confiável dos equipamentos industriais. Várias técnicas podem ser implementadas para otimizar o processo de manutenção e reduzir custos operacionais. A seguir, apresentamos algumas das principais técnicas para efetivar uma manutenção eficiente:
1. Planejamento e Programação: Um dos primeiros passos para uma manutenção eficiente é o planejamento adequado. Isso envolve a criação de um cronograma de manutenção que considere a frequência necessária para as paradas preventivas e corretivas, baseado no uso e na criticidade de cada equipamento. Um bom planejamento ajuda a evitar paradas inesperadas e garantirá que todos os recursos estejam disponíveis quando necessário.
2. Monitoramento Contínuo: O uso de tecnologias de monitoramento em tempo real permite acompanhar o desempenho dos equipamentos e identificar sinais de falhas antes que ocorram. Sensores podem ser instalados para coletar dados como temperatura, vibração e consumo de energia, fornecendo informações valiosas que contribuem para uma manutenção preditiva eficaz.
3. Treinamento da Equipe: A capacitação dos profissionais envolvidos na manutenção é fundamental. Equipes bem treinadas são mais capazes de diagnosticar problemas rapidamente, aplicar manutenções corretivas com eficácia e garantir que as práticas de segurança sejam seguidas. O investimento em treinamentos regulares resulta em funcionários mais confiantes e produtivos.
4. Consolidação de Manuais e Documentação: Manter documentação detalhada sobre os procedimentos de manutenção, manuais dos equipamentos e históricos de intervenções é vital. Isso não só facilita o trabalho da equipe de manutenção, como também permite a análise de dados históricos para identificar tendências e áreas de melhoria.
5. Implementação de Manutenção Condicionada: A manutenção condicionada se baseia no estado real do equipamento em determinado momento, em vez de seguir um calendário fixo. Isso significa que a manutenção só é realizada quando os dados de monitoramento indicam que é necessário, permitindo uma abordagem mais eficiente que pode reduzir custos e otimizar o tempo de operação.
6. Análise de Causa Raiz: Quando ocorrem falhas, é fundamental investigar e entender as causas subjacentes. A análise de causa raiz ajuda a identificar não apenas o que ocorreu, mas por que aconteceu, permitindo que as empresas adotem medidas corretivas adequadas e evitem a recorrência do problema.
Essas técnicas, quando implementadas em conjunto, podem levar a uma estratégia de manutenção robusta e eficiente. A satisfação nas operações e o aumento da produtividade são resultados diretos de uma abordagem proativa e bem estruturada.
Desafios Comuns na Manutenção Eletrônica
A manutenção eletrônica é essencial para a operação contínua das indústrias, mas enfrenta diversos desafios que podem impactar sua eficácia. Identificar e abordar esses desafios é fundamental para garantir o desempenho ideal dos equipamentos. Abaixo estão alguns dos desafios mais comuns enfrentados na manutenção eletrônica:
1. Falta de Recursos Financeiros: Muitas empresas enfrentam restrições orçamentárias que dificultam a implementação de programas de manutenção eficazes. A falta de investimentos pode resultar em manutenções inadequadas, equipamentos deteriorados e aumento do tempo de inatividade, o que leva a custos operacionais mais altos.
2. Escassez de Mão de Obra Qualificada: A alta demanda por profissionais qualificados em manutenção eletrônica resulta em uma escassez de mão de obra especializada. A falta de técnicos capacitados pode limitar a capacidade das empresas de realizar manutenções eficazes e oportunas, aumentando o risco de falhas nos sistemas eletrônicos.
3. Complexidade dos Sistemas Eletrônicos: Os avanços tecnológicos tornaram os sistemas eletrônicos mais complexos, dificultando o diagnóstico e a correção de problemas. Essa complexidade exige conhecimento técnico especializado e ferramentas adequadas, e a falta desses recursos pode atrasar as manutenções e levar a interrupções na produção.
4. Integração de Sistemas Antigos e Novos: Muitas indústrias operam com um mix de equipamentos antigos e novos. A integração de tecnologias legadas com sistemas mais modernos pode ser desafiadora, pois os novos equipamentos podem não ser compatíveis com as infraestruturas existentes. Isso pode dificultar as atividades de manutenção e aumentar o risco de falhas.
5. Resistência à Mudança: Em algumas organizações, há resistência à adoção de novas práticas de manutenção e tecnologias. Essa postura conservadora pode atrasar a implementação de métodos eficientes, como a manutenção preditiva e o uso de análise de dados, prejudicando a competitividade da empresa no mercado.
6. Falta de Dados e Documentação: A ausência de registros de manutenção e dados históricos pode dificultar a análise de falhas e a formulação de planos eficazes. Sem informações relevantes, as empresas têm dificuldades em identificar padrões de desgaste e prever eventuais problemas, comprometendo a eficácia das manutenções.
Embora esses desafios sejam comuns, abordá-los de forma proativa é essencial para garantir que a manutenção eletrônica se mantenha eficaz. Investir em treinamento, tecnologia e processos de manutenção pode mitigar muitos desses problemas, aumentando a eficiência e a confiabilidade das operações industriais.
Tecnologias Inovadoras para Suporte à Manutenção
A adoção de tecnologias inovadoras tem transformado a abordagem da manutenção eletrônica nas indústrias, proporcionando soluções que aumentam a eficiência e reduzem custos.
A seguir, exploraremos algumas das tecnologias mais relevantes que estão suportando a manutenção:
1. Internet das Coisas (IoT): A IoT permite que dispositivos e máquinas se comuniquem entre si e com sistemas de monitoramento centralizados. Sensores conectados em equipamentos podem coletar dados em tempo real sobre o desempenho, desgaste e condições operacionais, facilitando a manutenção preditiva. Com esses dados, as empresas podem planejar manutenções com base nas necessidades reais, evitando paradas inesperadas.
2. Manutenção Preditiva Baseada em Dados: Utilizando algoritmos de análise de dados e aprendizado de máquina, a manutenção preditiva se torna mais eficiente. Os dados históricos e em tempo real são analisados para identificar padrões de falhas e prever problemas futuros. Essa abordagem não só melhora a disponibilidade dos equipamentos, mas também trivializa o planejamento das atividades de manutenção.
3. Realidade Aumentada (RA): A RA está ganhando espaço na manutenção eletrônica ao permitir que os técnicos visualizem informações importantes diretamente no campo de visão através de dispositivos como óculos inteligentes. Isso os ajuda a realizar diagnósticos precisos e reparos com eficiência, já que podem acessar manuais, instruções e suporte remoto enquanto trabalham.
4. Drones e Robótica: Drones são utilizados para inspeções em locais de difícil acesso, como parte de sistemas de manutenção em grandes instalações industriais. Com câmeras de alta resolução e sensores, eles podem coletar dados e identificar falhas sem a necessidade de intervenções perigosas. A robótica, por sua vez, tem auxiliado na automação de tarefas, reduzindo a carga de trabalho humano e aumentando a precisão dos serviços de manutenção.
5. Software de Gestão de Manutenção (CMMS): Os sistemas de gestão de manutenção assistida por computador (CMMS) permitem às organizações monitorar, programar e rastrear atividades de manutenção de forma eficaz. Esses softwares oferecem uma visão clara sobre o status de equipamentos, históricos de manutenção e programação, facilitando a tomada de decisões informadas e otimizando recursos.
6. Impressão 3D: A impressão 3D está mudando a forma como as peças de reposição são fabricadas. Ao permitir que empresas criem peças sob demanda, essa tecnologia ajuda a reduzir os tempos de espera e os custos de armazenamento, além de facilitar a personalização de componentes para atender necessidades específicas.
Essas tecnologias inovadoras não apenas modernizam as práticas de manutenção eletrônica, mas também impulsionam as indústrias em direção à indústria 4.0, onde a eficiência e a capacidade de resposta são fundamentais. A adoção dessas tecnologias pode fornecer uma vantagem competitiva significativa ao oferecer melhores operações, menor tempo de inatividade e maior satisfação do cliente.
Em conclusão, a manutenção eletrônica desempenha um papel crucial na eficiência operacional e na continuidade dos processos industriais.
Os desafios enfrentados, como a falta de recursos financeiros e a complexidade dos sistemas, podem ser superados através da adoção de práticas eficazes e inovações tecnológicas.
Investir em manutenção preventiva, preditiva e técnicas de gestão eficientes não apenas aumenta a produtividade, mas também prolonga a vida útil dos equipamentos e garante a segurança das operações.
O futuro da manutenção eletrônica está ligado à integração de tecnologias inovadoras que oferecem maior confiabilidade e eficiência, posicionando as empresas de maneira competitiva no mercado.
Portanto, é essencial que as organizações reconheçam a importância de uma gestão de manutenção robusta e se adaptem às novas demandas do setor para prosperar em um ambiente cada vez mais desafiador.
Gostou? compartilhe!