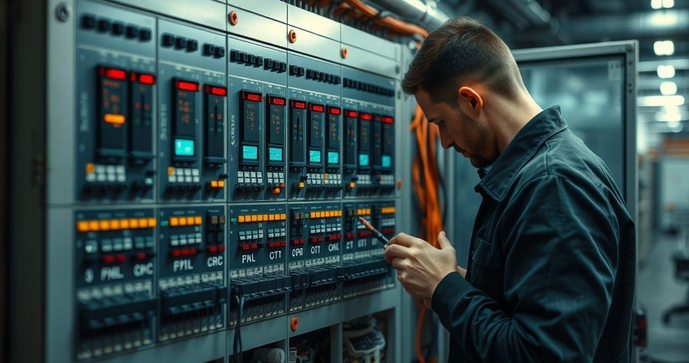
Importância da Manutenção em CLP para Sistemas Automatizados
A manutenção em CLP, ou Controlador Lógico Programável, é fundamental para a operação eficaz de sistemas automatizados. Esses dispositivos são o coração do controle industrial, gerenciando uma variedade de processos e máquinas com eficiência.
A importância da manutenção se reflete diretamente na redução de paradas inesperadas, que podem resultar em prejuízos significativos para as empresas. Uma falha no CLP pode interromper toda a linha de produção, causando atrasos e custos adicionais.
Além disso, a manutenção regular garante que os CLPs operem dentro dos padrões ideais, permitindo que as empresas maximizem o desempenho e a produtividade. Equipamentos bem mantidos têm menor probabilidade de falhar, o que contribui para uma operação mais fluida e eficiente.
Um aspecto crucial da manutenção é a prevenção de falhas, que envolve inspeções periódicas e testes de funcionalidade. Isso permite identificar problemas antes que se tornem críticos, garantindo que as intervenções necessárias sejam feitas de maneira planejada.
Além dos benefícios operacionais, a manutenção em CLP também é vital para a segurança dos trabalhadores. Um sistema que falha pode representar riscos, e a manutenção adequada ajuda a mitigar esses perigos, promovendo um ambiente de trabalho mais seguro.
Por fim, a manutenção em CLP pode aumentar a vida útil do equipamento, garantindo um melhor retorno sobre o investimento. Ao preservar a integridade dos CLPs, as empresas podem evitar gastos com substituições prematuras e prolongar a utilização desses ativos valiosos.
Principais Componentes do CLP e Suas Funcionalidades
Os Controladores Lógicos Programáveis (CLPs) são compostos por vários componentes essenciais que trabalham juntos para controlar processos industriais. Compreender esses componentes e suas funcionalidades é crucial para a manutenção adequada e o funcionamento eficiente do sistema.
Um dos principais componentes do CLP é a CPU (Unidade Central de Processamento), que atua como o cérebro do sistema. É responsável por executar o programa lógico, tomando decisões com base nas entradas recebidas e controlando as saídas de acordo. A performance da CPU é fundamental para um processamento ágil e preciso.
Outro componente vital é a memória, que armazena o programa de controle, dados operacionais e informações necessárias para o funcionamento do CLP. Existem diferentes tipos de memória, como RAM e ROM, cada uma com funções específicas que garantem a operação correta do sistema.
Os módulos de entrada e saída (I/O) também são componentes cruciais. Os módulos de entrada recebem sinais de dispositivos como sensores e botões, enquanto os módulos de saída enviam sinais para atuadores, como motores e válvulas. Esses módulos permitem a interface do CLP com o mundo externo e são fundamentais para a automação de processos.
Adicionalmente, muitos CLPs contam com portas de comunicação, que permitem a interação com outros dispositivos e sistemas, como supervisórios e rede industrial. A comunicação eficaz é essencial para monitoramento, controle remoto e integração de diferentes partes do sistema.
Por último, a fonte de alimentação é um componente indispensável, pois fornece a energia necessária para o funcionamento do CLP e de seus dispositivos associados. A utilização de uma fonte de alimentação estável e confiável é vital para garantir a continuidade da operação do sistema.
Etapas da Manutenção Preventiva em CLP
A manutenção preventiva em CLP é um conjunto de ações programadas que visam garantir o pleno funcionamento do equipamento e evitar falhas. Este processo envolve várias etapas que devem ser seguidas sistematicamente para assegurar a eficiência do sistema.
A primeira etapa consiste na planificação da manutenção. É essencial elaborar um cronograma que considere a frequência e a periodicidade das manutenções, levando em conta a criticidade dos processos controlados pelo CLP e as recomendações do fabricante.
Em seguida, a inspeção visual deve ser realizada para identificar qualquer sinal de desgaste, corrosão ou falhas externas nos componentes do CLP e na fiação. Essa inspeção permite detectar problemas associados ao ambiente em que o CLP está instalado.
Após a inspeção visual, é importante realizar testes de funcionalidade, onde devem ser verificados o desempenho da CPU, a resposta dos módulos de entrada e saída, e a eficácia das comunicações. Isso assegura que todos os componentes estão operando como esperado.
Uma etapa crucial é a limpeza dos componentes, principalmente aquelas áreas suscetíveis à acumulação de sujeira e poeira. A limpeza regular não apenas mantém a aparência do CLP, mas também evita o superaquecimento e outros problemas relacionados ao acúmulo de detritos.
Por fim, a etapa de documentação é fundamental. É necessário registrar todas as atividades de manutenção, incluindo inspeções, testes realizados e qualquer ajuste ou substituição de peças. Esse histórico permite acompanhar o desempenho do CLP ao longo do tempo e facilita futuras manutenções.
Sinais de Alerta para Manutenção Corretiva em CLP
Identificar sinais de alerta para a manutenção corretiva em um Controlador Lógico Programável (CLP) é crucial para evitar paradas inesperadas e garantir a continuidade das operações. Alguns sintomas podem indicar falhas iminentes ou a necessidade de intervenção técnica.
Um dos principais sinais de alerta é a inconsistência no funcionamento. Se o CLP apresenta respostas lentas ou inconsistentes, como atrasos na execução de comandos, isso pode indicar problemas na CPU ou na comunicação entre módulos. Monitorar essas inconsistências é vital para evitar falhas maiores.
Outro sinal importante é a presença de mensagens de erro no sistema. Muitos CLPs possuem LEDs indicadores ou displays que sinalizam falhas específicas. Prestar atenção a essas mensagens pode ajudar na rápida identificação dos problemas e na aplicação de soluções corretivas.
Além disso, ruídos anormais durante o funcionamento do CLP ou de seus componentes devem ser motivo de atenção. Sons estrondosos ou chiados podem sinalizar desgaste nas partes móveis ou falhas elétricas que necessitam de avaliação imediata.
A superaquecimento do dispositivo também é um sinal de alerta significativo. Se o CLP estiver excessivamente quente ao toque, isso pode indicar problemas na fonte de alimentação ou falhas internas. Monitorar a temperatura de operação é essencial para prevenir danos permanentes.
Por último, a falta de comunicação com outros dispositivos e sistemas pode ser um indicativo de falhas nos módulos de comunicação. Quando o CLP não consegue estabelecer conexão com sensores ou atuadores, é necessário realizar uma análise mais detalhada para identificar e resolver o problema.
Dicas para Garantir a Vida Útil do seu CLP
Garantir a vida útil de um Controlador Lógico Programável (CLP) é essencial para assegurar a continuidade e eficiência das operações industriais. Algumas dicas práticas podem ajudar a prolongar a durabilidade do equipamento e reduzir a necessidade de manutenções corretivas.
Primeiramente, é crucial realizar manutenções preventivas regularmente, seguindo um cronograma adequado. Inspeções frequentes e manutenção programada ajudam a identificar problemas antes que se tornem críticos, garantindo que o CLP opere em condições ideais.
Outra dica importante é monitorar as condições ambientais em que o CLP está instalado. Proteger o equipamento de umidade excessiva, poeira e temperaturas extremas pode prevenir danos que poderiam comprometer seu funcionamento.
Além disso, é essencial usar filtros e sistemas de proteção para bloquear partículas indesejadas e flutuações de energia. Filtros de linha de energia e disjuntores podem ajudar a proteger o CLP contra picos de tensão e falhas elétricas.
A limpeza regular dos componentes do CLP também é vital. Remover a poeira e a sujeira acumuladas previne o superaquecimento e outros problemas operacionais. Utilize métodos de limpeza apropriados, evitando o uso de líquidos que possam danificar as partes internas.
Por fim, garantir uma adequada formação e treinamento da equipe que opera o CLP contribui para seu uso seguro e eficiente. Profissionais familiarizados com as características e funcionamento do aparelho estão mais capazes de identificar problemas e realizar intervenções adequadas, preservando o equipamento por mais tempo.
Impactos da Falta de Manutenção em CLP na Produção
A falta de manutenção em um Controlador Lógico Programável (CLP) pode ter impactos significativos na produção industrial. Esses impactos não apenas afetam a eficiência das operações, mas também podem resultar em prejuízos financeiros substanciais.
Um dos impactos mais imediatos é a interrupção das operações. Quando um CLP falha devido à falta de manutenção, ele pode causar paradas inesperadas na linha de produção, resultando em perda de tempo e recursos. O retrabalho e as filas de espera podem acarretar custos elevados.
Além disso, a redução da qualidade dos produtos é uma consequência comum da falta de manutenção. Um CLP mal calibrado ou com componentes desgastados pode levar a erros na produção, resultando na fabricação de produtos com defeitos ou não conformidades que comprometem a satisfação do cliente.
A produtividade também é afetada diretamente. Com equipamentos operando de forma ineficiente, como resultado da falta de ajustes e limpezas necessárias, a taxa de produção pode cair, e as metas organizacionais podem não ser alcançadas. Isso prejudica a competitividade da empresa no mercado.
Outro aspecto a se considerar é o aumento dos custos operacionais. Falhas constantes exigem intervenções corretivas mais caras e inesperadas, além de potencialmente necessitar de substituições de equipamentos antes do tempo previsto. Esses custos adicionais podem impactar seriamente o orçamento da organização.
Por último, a falta de manutenção em CLPs pode prejudicar a segurança dos trabalhadores. Equipamentos que falham podem causar acidentes e o não cumprimento das normas de segurança, criando um ambiente de trabalho inseguro e aumentando o risco de lesões.
Em suma, a manutenção em Controladores Lógicos Programáveis (CLPs) é uma prática indispensável para garantir a eficiência e segurança nas operações industriais. Investir em manutenção preventiva não só prolonga a vida útil do equipamento, mas também evita interrupções na produção, melhora a qualidade dos produtos e reduz custos operacionais.
Os cuidados com os principais componentes do CLP, a identificação de sinais de alerta e a implementação de dicas práticas são fundamentais para assegurar um funcionamento contínuo e eficiente. Além disso, a falta de manutenção pode resultar em graves consequências, impactando a produtividade e a segurança do ambiente de trabalho.
Portanto, reconhecer a importância da manutenção regular e adotar práticas adequadas são passos essenciais para operar um sistema automatizado de forma eficaz, promovendo não apenas a sustentabilidade dos processos, mas também a prosperidade do negócio.
Gostou? compartilhe!