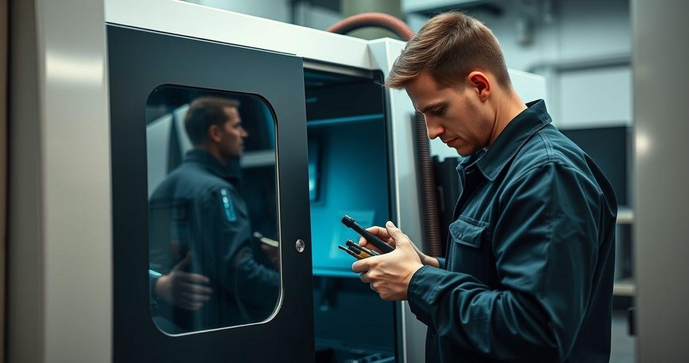
Importância da Manutenção de Máquinas CNC
A manutenção de máquinas CNC é um aspecto vital para a operação contínua e eficiente das fábricas e oficinas. Esses equipamentos complexos demandam atenção especial para garantir sua precisão e desempenho ao longo do tempo.
Uma das principais razões para realizar a manutenção regular é a prevenção de falhas. Máquinas CNC podem apresentar desgastes em suas peças devido ao uso intenso, o que pode resultar em paradas inesperadas e custos elevados com reparos. A manutenção preventiva ajuda a identificar e corrigir problemas antes que se tornem críticos.
Além disso, a manutenção adequada contribui para a qualidade do produto final. Com componentes bem ajustados e calibrados, as máquinas CNC operam com maior precisão, resultando em peças fabricadas que atendem aos padrões exigidos. Isso é especialmente importante em indústrias que lidam com tolerâncias rigorosas.
Outro fator a considerar é a segurança dos operadores. Máquinas mal conservadas podem representar riscos, como falhas que levam a acidentes. Realizar manutenções regulares garante que os sistemas de segurança estejam sempre funcionais, proporcionando um ambiente de trabalho mais seguro.
Por fim, a manutenção de máquinas CNC pode impactar significativamente a eficiência geral da produção. Programas de manutenção bem estruturados não apenas prolongam a vida útil dos equipamentos, mas também reduzem os custos operacionais ao evitar desperdícios gerados por falhas e ineficiências.
Principais Tipos de Manutenção para Máquinas CNC
Existem diversos tipos de manutenção que podem ser aplicados a máquinas CNC, cada um com suas características e objetivos específicos. Conhecer essas abordagens é fundamental para a implementação de uma estratégia que garanta o funcionamento adequado e eficiente dos equipamentos.
A seguir, destacamos os principais tipos de manutenção para máquinas CNC:
1. Manutenção Preventiva: Esta prática envolve a realização de tarefas programadas com o intuito de prevenir falhas e garantir que a máquina opere dentro dos parâmetros ideais. Inclui verificações regulares de calibragem, lubrificação, troca de peças desgastadas e limpeza de componentes. A manutenção preventiva é essencial para aumentar a vida útil das máquinas e minimizar o tempo de inatividade.
2. Manutenção Corretiva: É a intervenção realizada para corrigir falhas ou problemas já ocorridos. Geralmente, acontece quando um componente falha, resultando em paradas inesperadas. Embora seja importante, a manutenção corretiva pode levar a custos mais altos e perda de produtividade, já que a máquina fica fora de operação até que o problema seja resolvido.
3. Manutenção Preditiva: Utiliza tecnologias de monitoramento e análise de dados para prever quando uma falha pode ocorrer, permitindo que as equipes de manutenção realizem intervenções baseadas no estado real da máquina. Essa abordagem é eficiente, pois reduz os custos com manutenção desnecessária e melhora a confiabilidade do equipamento.
4. Manutenção Detectiva: Esta forma de manutenção é focada em identificar e diagnosticar problemas antes que resultem em falhas significativas. Envolve a análise de dados de desempenho, testes de funcionalidade e monitoramento de condições operacionais, ajudando as empresas a agir preventivamente.
5. Manutenção Total Produtiva (TPM): Este modelo envolve todos os funcionários na manutenção da máquina, promovendo uma cultura de responsabilidade compartilhada. O objetivo é maximizar a efetividade dos equipamentos por meio de manutenções autônomas realizadas por operadores, além de intervenções realizadas por profissionais especializados.
Compreender esses tipos de manutenção permite que as empresas planejem melhor suas estratégias e invistam de forma mais eficaz na conservação de suas máquinas CNC, garantindo alta performance e segurança na operação.
Passos para uma Manutenção Preventiva Eficiente
Implementar uma manutenção preventiva eficiente para máquinas CNC é fundamental para maximizar sua performance e prolongar a vida útil dos equipamentos. A seguir, apresentamos os passos essenciais para realizar uma manutenção preventiva de forma eficaz:
1. Estabelecimento de um Cronograma de Manutenção: O primeiro passo é criar um cronograma detalhado definindo a frequência das inspeções e dos serviços necessários. Esse cronograma deve ser elaborado com base nas recomendações do fabricante e na quantidade de uso da máquina.
2. Treinamento da Equipe: Garantir que toda a equipe envolvida na operação e manutenção das máquinas esteja devidamente treinada é crucial. Isso inclui operadores e técnicos responsáveis pela manutenção, que devem conhecer os procedimentos adequados e as melhores práticas de cuidados com equipamentos CNC.
3. Monitoramento e Registro das Condições Operacionais: É importante registrar todos os dados operacionais, como horas de funcionamento, ciclos de produção e ocorrências de falhas. Esses dados ajudarão a identificar padrões e determinar quando a manutenção deve ser realizada.
4. Inspeção Regular de Componentes: Realizar inspeções frequentes em partes-chave da máquina, como eixos, conversores e sistemas de lubrificação, é essencial. Durante as inspeções, verifique o estado de cada componente e faça a limpeza necessária para evitar acúmulo de sujeira e outros detritos.
5. Lubrificação Adequada: A lubrificação é um aspecto fundamental da manutenção preventiva. Certifique-se de que todos os pontos de lubrificação sejam atendidos conforme as recomendações do fabricante, utilizando os lubrificantes apropriados para cada tipo de componente.
6. Substituição de Partes Desgastadas: Identifique e substitua peças que demonstram sinais de desgaste antes que elas causem falhas. Isso pode incluir rolamentos, correias, ferramentas de corte ou outros componentes críticos.
7. Validação e Testes Após a Manutenção: Após realizar qualquer serviço de manutenção, é importante validar o funcionamento da máquina. Testes devem ser feitos para garantir que todos os sistemas estejam operando corretamente antes de retomar a produção.
8. Revisão e Ajustes do Cronograma: Por fim, revise periodicamente o cronograma de manutenção e ajuste-o conforme necessário, com base na experiência adquirida e na análise dos dados coletados. Essa prática garantirá uma manutenção sempre alinhada às necessidades reais das máquinas CNC.
Ao seguir esses passos, as empresas podem assegurar que suas máquinas CNC permaneçam em ótimo estado de funcionamento, reduzindo paradas inesperadas e aumentando a eficiência operacional.
Erros Comuns na Manutenção de Máquinas CNC
A manutenção de máquinas CNC é essencial para garantir sua eficiência e durabilidade, mas existem erros comuns que podem comprometer a eficácia deste processo. Conhecer essas armadilhas é crucial para que as empresas possam evitá-las. A seguir, apresentamos alguns dos erros mais frequentes na manutenção de máquinas CNC:
1. Falta de Planejamento: Um dos principais erros é não ter um plano de manutenção bem definido. Sem um cronograma claro e procedimentos de manutenção, as máquinas podem acabar sendo negligenciadas, resultando em falhas inesperadas e aumentos de custos operacionais.
2. Ignorar Recomendações do Fabricante: Muitos técnicos e operadores podem subestimar a importância das diretrizes do fabricante. Ignorar as recomendações sobre manutenção, como prazos e procedimentos específicos, pode levar a problemas sérios e à perda de garantias.
3. Realização de Manutenção Apenas Quando Necessário: A manutenção corretiva é frequentemente um reflexo da falta de uma estratégia preventiva. Esperar que algo quebre antes de agir pode resultar em paradas longas e custos inesperados.
4. Não Documentar a Manutenção Realizada: A falta de registros de manutenção pode levar a um ciclo vicioso de problemas não resolvidos. Documentar as atividades de manutenção ajuda a identificar padrões de falhas e a programar intervenções futuras de maneira mais eficaz.
5. Não Treinar a Equipe Adequadamente: Subestimar a importância do treinamento para os operadores e técnicos é um erro que pode comprometer a segurança e a eficiência operacional. Equipamentos complexos, como máquinas CNC, exigem que os funcionários compreendam como operar e manter esses sistemas corretamente.
6. Ignorar Sinais de Alerta: Muitos profissionais tendem a ignorar sinais de desgaste ou funcionamento irregular das máquinas, como ruídos anormais ou vibrações intensas. Esses sintomas, se não tratados, podem levar a falhas graves e interrupções na produção.
7. Uso de Peças de Reposição de Qualidade Inferior: A substituição de componentes com peças de baixa qualidade pode comprometer a operação da máquina e resultar em falhas adicionais. Sempre opte por peças recomendadas pelo fabricante ou de fornecedores de confiança.
8. Falta de Manutenção nos Sistemas Auxiliares: Muitas vezes, a atenção é concentrada na máquina principal, enquanto sistemas auxiliares, como o de lubrificação, refrigeradores ou sensores, são negligenciados. A manutenção desses sistemas é tão importante quanto a da máquina principal.
Identificar e corrigir esses erros pode fazer uma grande diferença no desempenho e na vida útil das máquinas CNC. A implementação de boas práticas de manutenção garantirá uma operação mais eficiente e segura, contribuindo para o sucesso a longo prazo da produção.
Como Monitorar a Performance de Máquinas CNC
Monitorar a performance de máquinas CNC é um aspecto crucial para manter a eficiência operacional e garantir que os equipamentos atendam às expectativas de produção.
A seguir, apresentamos algumas estratégias e ferramentas para realizar um monitoramento eficaz:
1. Uso de Sistemas de Monitoramento em Tempo Real: Implementar softwares de monitoramento em tempo real permite que as empresas acompanhem a performance das máquinas instantaneamente. Esses sistemas podem oferecer dados sobre tempo de ciclo, produtividade e períodos de inatividade, ajudando a tomar decisões informadas.
2. Indicadores de Desempenho (KPIs): Estabelecer KPIs específicos para máquinas CNC é fundamental. Métricas como a disponibilidade, taxa de produção, eficiência geral do equipamento (OEE) e qualidade das peças produzidas são essenciais para medir a performance. Acompanhá-las regularmente permite identificar áreas que precisam de atenção.
3. Coleta de Dados Históricos: Armazenar e analisar dados históricos sobre a operação das máquinas ajuda a detectar padrões e tendências. Através da análise de dados passados, é possível antecipar problemas, planejar manutenções e otimizar processos.
4. Sensores e Monitoramento de Condição: Equipar máquinas CNC com sensores que monitoram condições como temperatura, vibração e pressão é uma excelente forma de coletar informações sobre seu funcionamento. Esses sensores podem proporcionar alertas precoces sobre possíveis falhas, permitindo ações corretivas antes que problemas sérios ocorram.
5. Inspeções Regulares e Manuais de Checklist: Realizar inspeções regulares e usar checklists podem ajudar a validar se a máquina está operando conforme esperado. Durante essas inspeções, verifique componentes chave, lubrificação, e dados operacionais para garantir que tudo está dentro dos padrões estabelecidos.
6. Feedback dos Operadores: Os operadores que trabalham diretamente com as máquinas são uma fonte valiosa de informações. Incentivar uma cultura onde os operadores reportem problemas ou inconsistências percebidas no funcionamento das máquinas é fundamental para mantê-las em bom estado. Isso também contribui para a melhoria contínua dos processos.
7. Análise de Causa Raiz: Quando problemas de performance são identificados, é importante realizar uma análise de causa raiz para entender as origens das falhas. Ao abordar a causa base, as empresas podem implementar soluções que evitem a recorrência dos problemas.
Ao adotar essas estratégias de monitoramento, as empresas podem garantir que suas máquinas CNC operem com a máxima eficiência, minimizando custos e melhorando continuamente a qualidade da produção.
Benefícios da Manutenção Regular em Máquinas CNC
A manutenção regular em máquinas CNC traz uma série de benefícios significativos que impactam diretamente na eficiência, segurança e rentabilidade das operações. A seguir, elencamos os principais benefícios dessa prática:
1. Aumento da Vida Útil dos Equipamentos: Realizar manutenções periódicas garante que os componentes das máquinas operem de maneira adequada, minimizando o desgaste e, consequentemente, prolongando a vida útil dos equipamentos. Isso reduz a necessidade de substituições frequentes, resultando em economias relevantes.
2. Melhoria na Precissão das Peças Produzidas: Máquinas bem mantidas são capazes de operar com maior precisão, resultando na fabricação de peças com qualidade consistente e dentro das especificações. Isso é especialmente crítico em indústrias onde a precisão é vital, como na aeronáutica e na medicina.
3. Redução de Paradas Não Planejadas: A manutenção preventiva ajuda a identificar e resolver problemas antes que se tornem críticos, evitando interrupções inesperadas na produção. Isso não apenas minimiza os custos associados às paradas, mas também melhora a eficiência geral do processo produtivo.
4. Economia nos Custos Operacionais: Manter máquinas em boas condições garante uma operação mais eficiente. Máquinas que funcionam adequadamente geralmente consomem menos energia e recursos, além de demandarem menos intervenções corretivas, resultando em menores custos operacionais a longo prazo.
5. Maior Segurança para os Operadores: A realização de manutenções regulares é essencial para garantir a segurança no ambiente de trabalho. Equipamentos em bom estado apresentam menos riscos de falhas que podem causar acidentes, protegendo assim os operadores e evitando possíveis responsabilidades legais.
6. Valorização do Ativo da Empresa: Um programa de manutenção eficiente contribui para a valorização dos ativos industriais. Máquinas bem mantidas tendem a ter um melhor valor de revenda e atraem mais interesse em processos de aquisição ou financiamento.
7. Otimização da Produtividade: Ao garantir que as máquinas funcionem sem interrupções e em sua capacidade ideal, as empresas podem otimizar sua produtividade. Isso resulta em mais unidades produzidas em menor tempo, aumentando a competitividade no mercado.
Em resumo, os benefícios da manutenção regular em máquinas CNC vão muito além da simples preservação do equipamento. Essa prática é uma estratégia vital que impacta diretamente nos resultados financeiros, na segurança dos colaboradores e na qualidade dos produtos fabricados, contribuindo para um ambiente industrial mais eficiente e sustentável.
A manutenção de máquinas CNC é uma prática imprescindível para garantir eficiência, segurança e durabilidade dos equipamentos.
Através da implementação de estratégias adequadas, como a manutenção preventiva, o monitoramento constante e o treinamento adequado da equipe, as empresas podem evitar falhas inesperadas, reduzir custos operacionais e manter a qualidade dos produtos.
Os benefícios gerados por uma rotina de manutenção eficaz são significativos e impactam positivamente na produtividade e competitividade no mercado.
Portanto, investir em manutenção regular é uma escolha inteligente que assegura não apenas o valor dos ativos, mas também o sucesso a longo prazo das operações industriais.
Gostou? compartilhe!