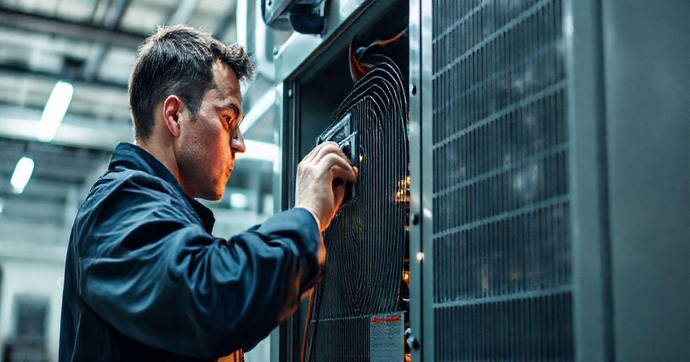
O conserto de inversor Weg é uma prática fundamental para garantir a eficiência e a durabilidade dos equipamentos em diversas aplicações industriais. Compreender os sinais de falha e saber como realizar a manutenção adequada pode evitar paradas inesperadas e custos elevados. Neste artigo, abordaremos dicas valiosas e soluções eficazes para o conserto de inversores Weg, ajudando você a manter seu sistema em perfeito funcionamento.
1. Principais Sinais de Falha em Inversores Weg
Os inversores Weg são amplamente utilizados em diversas aplicações industriais, proporcionando controle eficiente de motores elétricos. No entanto, como qualquer equipamento eletrônico, eles podem apresentar falhas ao longo do tempo. Identificar os sinais de falha precocemente é crucial para evitar danos maiores e garantir a continuidade das operações. A seguir, discutiremos os principais sinais de falha que podem indicar problemas em inversores Weg.
Um dos primeiros sinais de falha que os operadores podem notar é a inconsistência no desempenho do motor. Se o motor não estiver funcionando em sua capacidade total ou se houver variações inesperadas na velocidade, isso pode ser um indicativo de que o inversor está enfrentando problemas. Essa inconsistência pode ser causada por falhas internas no inversor, como problemas na placa de controle ou na fonte de alimentação.
Outro sinal importante a ser observado é o aquecimento excessivo do inversor. Todos os inversores geram calor durante a operação, mas se o equipamento estiver superaquecendo, isso pode ser um sinal de que algo não está funcionando corretamente. O superaquecimento pode ser causado por uma ventilação inadequada, sobrecarga do motor ou falhas nos componentes internos. É essencial monitorar a temperatura do inversor e garantir que ele esteja operando dentro das especificações recomendadas pelo fabricante.
Além disso, ruídos anormais durante a operação do inversor também são um sinal de alerta. Se o inversor começar a emitir sons estranhos, como zumbidos, estalos ou cliques, isso pode indicar problemas mecânicos ou elétricos. Esses ruídos podem ser causados por componentes soltos, falhas nos circuitos ou até mesmo problemas com o motor conectado. Ignorar esses sinais pode levar a danos mais sérios e custos de reparo elevados.
Outro aspecto a ser considerado é a presença de mensagens de erro no display do inversor. Muitos modelos de inversores Weg possuem sistemas de diagnóstico que exibem códigos de erro quando detectam falhas. Esses códigos podem fornecer informações valiosas sobre a natureza do problema, permitindo que os técnicos realizem diagnósticos mais precisos. É fundamental consultar o manual do usuário para entender o significado dos códigos de erro e tomar as medidas corretivas necessárias.
Além dos sinais mencionados, a interrupção repentina do funcionamento do inversor é um dos sinais mais críticos de falha. Se o inversor parar de funcionar sem aviso prévio, isso pode ser um indicativo de falhas graves, como problemas na fonte de alimentação ou na placa de controle. Nesse caso, é essencial realizar uma verificação imediata para identificar a causa da interrupção e evitar danos adicionais ao sistema.
Outro sinal que não deve ser ignorado é a flutuação na tensão de saída. Se a tensão de saída do inversor estiver variando de forma irregular, isso pode afetar o desempenho do motor e causar danos a outros componentes do sistema. Flutuações na tensão podem ser causadas por problemas na rede elétrica, falhas no inversor ou até mesmo por conexões soltas. Monitorar a tensão de saída é fundamental para garantir a operação segura e eficiente do sistema.
Por fim, a falta de resposta aos comandos também é um sinal de que o inversor pode estar apresentando falhas. Se o inversor não responder aos comandos de controle, como iniciar ou parar o motor, isso pode indicar problemas na interface de controle ou na comunicação entre o inversor e o sistema de automação. Verificar as conexões e a configuração do sistema é essencial para resolver esse tipo de problema.
Identificar os sinais de falha em inversores Weg é fundamental para garantir a eficiência e a segurança das operações industriais. Ao observar inconsistências no desempenho, superaquecimento, ruídos anormais, mensagens de erro, interrupções repentinas, flutuações na tensão de saída e falta de resposta aos comandos, os operadores podem tomar medidas preventivas para evitar danos maiores e custos de reparo. Além disso, para sistemas que utilizam interfaces homem-máquina, como o Ihm rockwell , é importante garantir que a comunicação entre os dispositivos esteja funcionando corretamente, pois isso pode impactar diretamente o desempenho do inversor.
Em resumo, a atenção aos sinais de falha em inversores Weg é essencial para a manutenção adequada e a operação contínua dos sistemas industriais. Realizar inspeções regulares e estar atento a qualquer anomalia pode ajudar a prolongar a vida útil do equipamento e garantir a eficiência das operações.
2. Passo a Passo para Diagnosticar Problemas
Diagnosticar problemas em inversores Weg é uma tarefa essencial para garantir a continuidade das operações e a eficiência dos sistemas industriais. Um diagnóstico preciso pode evitar paradas inesperadas e custos elevados com reparos. A seguir, apresentamos um passo a passo para ajudá-lo a identificar e resolver problemas comuns em inversores Weg.
Passo 1: Verificação Visual
O primeiro passo no diagnóstico de problemas é realizar uma verificação visual do inversor. Inspecione o equipamento em busca de sinais visíveis de danos, como queimaduras, componentes soltos ou fios danificados. Verifique também se há acúmulo de poeira ou sujeira, que pode afetar o desempenho do inversor. Uma limpeza adequada pode ser necessária para garantir que o equipamento funcione corretamente.
Passo 2: Conferir Conexões Elétricas
Após a verificação visual, o próximo passo é conferir as conexões elétricas. Certifique-se de que todos os cabos estejam firmemente conectados e que não haja fios soltos ou danificados. Conexões mal feitas podem causar falhas no funcionamento do inversor. Utilize um multímetro para verificar a continuidade das conexões e garantir que a energia esteja sendo fornecida corretamente ao inversor.
Passo 3: Análise de Códigos de Erro
Se o inversor estiver apresentando mensagens de erro, consulte o manual do usuário para entender o significado dos códigos exibidos. Os códigos de erro podem fornecer informações valiosas sobre a natureza do problema. Anote os códigos e siga as orientações do fabricante para resolver as falhas identificadas. Essa etapa é crucial, pois pode direcionar o diagnóstico para áreas específicas do inversor.
Passo 4: Teste de Funcionamento
Realize um teste de funcionamento do inversor. Ligue o equipamento e observe seu desempenho. Verifique se o motor conectado está operando corretamente e se não há variações inesperadas na velocidade ou no torque. Durante o teste, preste atenção a ruídos anormais, aquecimento excessivo ou qualquer outro sinal que possa indicar problemas. Se o inversor não responder aos comandos, isso pode ser um sinal de falha na interface de controle.
Passo 5: Medição de Tensão e Corrente
Utilize um multímetro para medir a tensão e a corrente de saída do inversor. Compare os valores medidos com as especificações do fabricante. Se a tensão ou a corrente estiverem fora dos limites recomendados, isso pode indicar problemas no inversor ou no motor conectado. Essa medição é fundamental para garantir que o sistema esteja operando dentro das condições ideais.
Passo 6: Verificação de Componentes Internos
Se os passos anteriores não identificaram o problema, pode ser necessário abrir o inversor para verificar os componentes internos. Inspecione a placa de circuito, os capacitores e outros componentes eletrônicos em busca de sinais de danos, como inchaços ou vazamentos. Se você não tiver experiência em trabalhar com componentes eletrônicos, é recomendável consultar um profissional qualificado para evitar danos adicionais ao equipamento.
Passo 7: Teste de Sensores e Dispositivos de Proteção
Os inversores Weg geralmente possuem sensores e dispositivos de proteção que garantem a segurança do sistema. Verifique se os sensores estão funcionando corretamente e se não há obstruções que possam afetar seu desempenho. Teste os dispositivos de proteção, como fusíveis e relés, para garantir que estejam operando conforme o esperado. Se algum desses componentes estiver com defeito, pode ser necessário substituí-lo.
Passo 8: Consultar o Manual do Usuário
Durante o processo de diagnóstico, é sempre útil consultar o manual do usuário do inversor. O manual pode fornecer informações detalhadas sobre a configuração, manutenção e solução de problemas específicos do modelo em questão. Além disso, muitos manuais incluem tabelas de códigos de erro e orientações para resolução de problemas, o que pode facilitar o diagnóstico.
Passo 9: Considerar a Manutenção Profissional
Se, após seguir todos os passos acima, o problema persistir, pode ser necessário considerar a Manutenção em inversores de frequencia por um profissional qualificado. Técnicos especializados têm o conhecimento e as ferramentas necessárias para diagnosticar e reparar problemas complexos que podem não ser evidentes durante uma verificação básica. Além disso, a manutenção regular por profissionais pode ajudar a prevenir falhas futuras e prolongar a vida útil do equipamento.
Em resumo, diagnosticar problemas em inversores Weg requer uma abordagem sistemática e cuidadosa. Seguir este passo a passo pode ajudar a identificar e resolver problemas comuns, garantindo a eficiência e a segurança das operações industriais. A atenção aos detalhes e a realização de testes regulares são fundamentais para manter o desempenho ideal do inversor e evitar paradas inesperadas.
3. Ferramentas Necessárias para o Conserto
Realizar o conserto de inversores Weg requer um conjunto específico de ferramentas que garantem a eficácia e a segurança durante o processo. Ter as ferramentas adequadas à disposição não apenas facilita o trabalho, mas também minimiza o risco de danos ao equipamento. A seguir, apresentamos uma lista das ferramentas essenciais para o conserto de inversores, além de algumas dicas sobre como utilizá-las corretamente.
1. Multímetro
O multímetro é uma das ferramentas mais importantes para diagnosticar problemas em inversores. Ele permite medir tensão, corrente e resistência, fornecendo informações cruciais sobre o estado elétrico do equipamento. Ao usar um multímetro, é fundamental seguir as instruções do fabricante e garantir que o dispositivo esteja configurado corretamente para a medição desejada. Um multímetro digital é recomendado, pois oferece leituras mais precisas e fáceis de interpretar.
2. Chave de Fenda e Chave Allen
As chaves de fenda e as chaves Allen são essenciais para abrir o invólucro do inversor e acessar os componentes internos. É importante ter um conjunto de chaves de diferentes tamanhos para garantir que você possa trabalhar em diversos modelos de inversores. Ao desmontar o equipamento, tenha cuidado para não danificar os parafusos ou as roscas, e sempre mantenha as peças organizadas para facilitar a remontagem.
3. Pinças e Alicates
Pinças e alicates são ferramentas úteis para manusear componentes pequenos e delicados dentro do inversor. As pinças de ponta fina são especialmente úteis para alcançar áreas de difícil acesso e para segurar pequenos componentes durante a soldagem ou substituição. Os alicates de corte também são importantes para remover fios ou componentes danificados. Sempre utilize essas ferramentas com cuidado para evitar danos aos circuitos.
4. Ferro de Solda
Um ferro de solda é indispensável para realizar reparos em componentes eletrônicos, como resistores, capacitores e circuitos integrados. Ao utilizar o ferro de solda, é importante ter um bom controle da temperatura e usar solda de qualidade para garantir conexões duráveis. Além disso, é recomendável ter um suporte para o ferro de solda e um esponja úmida para limpar a ponta entre as soldagens.
5. Fonte de Alimentação Variável
Uma fonte de alimentação variável é uma ferramenta valiosa para testar o inversor após a realização de reparos. Ela permite fornecer diferentes níveis de tensão e corrente ao equipamento, facilitando a verificação do funcionamento correto. Ao usar a fonte de alimentação, é importante monitorar as leituras e garantir que o inversor esteja operando dentro das especificações recomendadas pelo fabricante.
6. Câmera Termográfica
A câmera termográfica é uma ferramenta avançada que permite identificar pontos quentes em componentes eletrônicos, ajudando a diagnosticar problemas de superaquecimento. Essa ferramenta é especialmente útil para detectar falhas em circuitos que podem não ser visíveis a olho nu. Ao utilizar uma câmera termográfica, é importante seguir as diretrizes do fabricante e interpretar corretamente as imagens para identificar áreas problemáticas.
7. Equipamentos de Proteção Individual (EPIs)
Ao realizar consertos em inversores, a segurança deve ser sempre uma prioridade. O uso de Equipamentos de Proteção Individual (EPIs), como luvas, óculos de proteção e, em alguns casos, máscaras, é fundamental para proteger o técnico de possíveis riscos, como queimaduras, cortes ou exposição a produtos químicos. Certifique-se de que todos os EPIs estejam em boas condições e adequados para o trabalho a ser realizado.
8. Software de Diagnóstico
Alguns inversores Weg podem ser conectados a softwares de diagnóstico que ajudam a identificar problemas e monitorar o desempenho do equipamento. Esses softwares podem fornecer informações detalhadas sobre o funcionamento do inversor, além de permitir a configuração de parâmetros e a atualização de firmware. É importante ter acesso ao software correto para o modelo específico do inversor que está sendo reparado.
9. Manual do Usuário
O manual do usuário é uma ferramenta essencial que deve estar sempre à mão durante o conserto. Ele contém informações valiosas sobre a configuração, manutenção e solução de problemas do inversor. Além disso, muitos manuais incluem diagramas e esquemas elétricos que podem facilitar o diagnóstico e a reparação. Consulte o manual frequentemente para garantir que você está seguindo as diretrizes do fabricante.
10. Materiais de Reposição
Por fim, é importante ter um estoque de materiais de reposição, como capacitores, resistores e outros componentes eletrônicos, que podem ser necessários durante o conserto. Ter esses materiais à disposição pode acelerar o processo de reparo e evitar atrasos na manutenção do equipamento. Ao adquirir peças de reposição, certifique-se de que elas sejam compatíveis com o modelo do inversor em questão.
Em resumo, ter as ferramentas necessárias para o conserto de inversores Weg é fundamental para garantir a eficácia e a segurança do trabalho. Desde multímetros e ferros de solda até EPIs e manuais do usuário, cada ferramenta desempenha um papel importante no diagnóstico e na reparação de problemas. Além disso, para aqueles que lidam com componentes eletrônicos, o Conserto de placas eletrônicas é uma parte essencial do processo, e ter as ferramentas adequadas pode fazer toda a diferença na qualidade do serviço prestado.
4. Manutenção Preventiva para Inversores Weg
A manutenção preventiva é uma prática essencial para garantir o funcionamento eficiente e prolongar a vida útil dos inversores Weg. Ao adotar um programa de manutenção preventiva, os operadores podem identificar e corrigir problemas antes que se tornem falhas graves, evitando paradas inesperadas e custos elevados com reparos. A seguir, apresentamos as principais práticas de manutenção preventiva que devem ser implementadas para garantir o desempenho ideal dos inversores.
1. Inspeções Visuais Regulares
Realizar inspeções visuais regulares é o primeiro passo na manutenção preventiva. Os operadores devem verificar o estado físico do inversor, procurando por sinais de desgaste, danos ou corrosão. É importante observar componentes como conectores, cabos e dissipadores de calor. Qualquer anomalia deve ser registrada e tratada imediatamente para evitar problemas futuros.
2. Limpeza do Equipamento
A sujeira e o acúmulo de poeira podem afetar o desempenho do inversor, causando superaquecimento e falhas. Portanto, é fundamental realizar a limpeza do equipamento regularmente. Utilize um pano seco e, se necessário, um aspirador de pó para remover a poeira acumulada. Evite o uso de líquidos ou produtos químicos que possam danificar os componentes eletrônicos. A limpeza deve ser feita com o inversor desligado e desconectado da fonte de energia.
3. Verificação das Conexões Elétricas
As conexões elétricas devem ser verificadas periodicamente para garantir que estejam firmes e livres de corrosão. Conexões soltas podem causar falhas intermitentes e danos ao inversor. Utilize um multímetro para testar a continuidade das conexões e certifique-se de que não há sinais de desgaste nos cabos. Se alguma conexão estiver danificada, ela deve ser reparada ou substituída imediatamente.
4. Monitoramento da Temperatura
O monitoramento da temperatura do inversor é uma prática importante na manutenção preventiva. O superaquecimento pode ser um sinal de problemas internos, como ventilação inadequada ou sobrecarga. Utilize termômetros ou câmeras termográficas para monitorar a temperatura do inversor durante a operação. Se a temperatura exceder os limites recomendados pelo fabricante, é necessário investigar a causa e tomar as medidas corretivas apropriadas.
5. Testes de Funcionamento
Realizar testes de funcionamento regulares é essencial para garantir que o inversor esteja operando corretamente. Ligue o equipamento e observe seu desempenho, verificando se o motor conectado está funcionando conforme esperado. Preste atenção a ruídos anormais, vibrações excessivas ou qualquer outro sinal que possa indicar problemas. Caso sejam identificadas anomalias, é importante realizar um diagnóstico detalhado.
6. Atualização de Firmware
Alguns inversores Weg possuem a capacidade de serem atualizados com novas versões de firmware. Essas atualizações podem incluir melhorias de desempenho, correções de bugs e novas funcionalidades. Verifique regularmente se há atualizações disponíveis e siga as instruções do fabricante para realizar a atualização. Manter o firmware atualizado é uma parte importante da manutenção preventiva, pois pode ajudar a evitar problemas futuros.
7. Manutenção de Placas Eletrônicas
A Manutenção de placas eletrônicas é uma parte crucial da manutenção preventiva dos inversores. As placas eletrônicas são componentes sensíveis que podem ser afetados por fatores como umidade, temperatura e vibrações. Realize inspeções regulares nas placas, verificando se há sinais de danos, como queimaduras ou componentes soltos. Se necessário, faça a limpeza das placas com ar comprimido para remover poeira e sujeira acumulada.
8. Registro de Manutenção
Manter um registro detalhado de todas as atividades de manutenção é fundamental para a gestão eficaz dos inversores. Registre as datas das inspeções, as ações realizadas e quaisquer problemas identificados. Esse registro pode ser útil para identificar padrões de falhas e planejar futuras manutenções. Além disso, um histórico de manutenção pode ser valioso para auditorias e para garantir a conformidade com as normas de segurança.
9. Treinamento da Equipe
Investir no treinamento da equipe responsável pela manutenção dos inversores é essencial para garantir que as práticas de manutenção preventiva sejam seguidas corretamente. A equipe deve estar ciente das melhores práticas, dos procedimentos de segurança e das especificações do fabricante. O treinamento contínuo ajuda a manter a equipe atualizada sobre novas tecnologias e técnicas de manutenção.
10. Consultas a Profissionais Especializados
Por fim, é recomendável consultar profissionais especializados para realizar manutenções mais complexas ou para obter orientações sobre a manutenção preventiva. Técnicos qualificados podem oferecer insights valiosos e ajudar a identificar problemas que podem não ser evidentes durante uma inspeção visual. Além disso, eles podem realizar reparos e ajustes que garantam o funcionamento ideal do inversor.
Em resumo, a manutenção preventiva para inversores Weg é uma prática essencial que pode prolongar a vida útil do equipamento e garantir seu funcionamento eficiente. Ao seguir as práticas mencionadas, os operadores podem identificar e corrigir problemas antes que se tornem falhas graves, evitando paradas inesperadas e custos elevados com reparos. A atenção aos detalhes e a implementação de um programa de manutenção regular são fundamentais para garantir a eficiência e a segurança das operações industriais.
5. Quando Chamar um Profissional Especializado
Identificar o momento certo para chamar um profissional especializado para o conserto de inversores Weg é crucial para garantir a eficiência e a segurança das operações industriais. Embora muitos problemas possam ser diagnosticados e resolvidos internamente, existem situações em que a experiência e o conhecimento de um técnico qualificado são indispensáveis. A seguir, discutiremos os principais sinais que indicam a necessidade de assistência profissional.
1. Falhas Intermitentes
Se o inversor apresentar falhas intermitentes, como desligamentos inesperados ou variações na velocidade do motor, é um sinal claro de que algo não está funcionando corretamente. Esses problemas podem ser difíceis de diagnosticar, pois podem não ocorrer de forma consistente. Um profissional especializado possui as ferramentas e o conhecimento necessários para identificar a causa raiz dessas falhas e realizar os reparos adequados.
2. Códigos de Erro Complexos
Os inversores Weg geralmente exibem códigos de erro quando detectam falhas. Se você se deparar com códigos de erro que não consegue interpretar ou que não estão documentados no manual do usuário, é hora de chamar um especialista. Esses profissionais têm experiência em lidar com uma variedade de códigos de erro e podem diagnosticar rapidamente o problema, evitando tentativas de conserto que podem agravar a situação.
3. Superaquecimento Persistente
O superaquecimento é um problema sério que pode danificar permanentemente o inversor. Se você notar que o equipamento está superaquecendo, mesmo após a limpeza e verificação das conexões, é fundamental buscar a ajuda de um profissional. O técnico pode realizar uma análise detalhada do sistema de ventilação, verificar a carga do motor e identificar quaisquer falhas internas que possam estar contribuindo para o problema.
4. Ruídos Anormais
Ruídos estranhos, como zumbidos, estalos ou cliques, podem ser sinais de problemas mecânicos ou elétricos. Se o inversor começar a emitir sons incomuns, é aconselhável consultar um especialista. Esses ruídos podem indicar desgaste em componentes internos, problemas com o motor ou falhas na placa de controle. Um técnico qualificado pode diagnosticar a origem do ruído e realizar os reparos necessários para evitar danos adicionais.
5. Dificuldades na Configuração
Se você estiver enfrentando dificuldades para configurar o inversor ou ajustar os parâmetros de operação, pode ser útil chamar um profissional. A configuração inadequada pode levar a problemas de desempenho e até mesmo a falhas no equipamento. Um especialista pode ajudar a garantir que o inversor esteja configurado corretamente para atender às necessidades específicas da aplicação, otimizando seu desempenho.
6. Danos Visíveis
Se houver danos visíveis no inversor, como queimaduras, componentes soltos ou sinais de corrosão, é essencial buscar a ajuda de um profissional. Esses danos podem afetar o funcionamento do equipamento e, se não forem tratados adequadamente, podem levar a falhas mais graves. Um técnico especializado pode avaliar a extensão dos danos e realizar os reparos necessários para restaurar o inversor à sua condição ideal.
7. Falta de Experiência ou Conhecimento
Se você ou sua equipe não têm experiência ou conhecimento suficiente para lidar com problemas complexos de inversores, é sempre melhor chamar um profissional. Tentar consertar um equipamento sem o conhecimento adequado pode resultar em danos adicionais e custos mais altos. Um técnico qualificado possui a formação e a experiência necessárias para realizar diagnósticos precisos e reparos eficazes.
8. Necessidade de Manutenção Especializada
Alguns problemas podem exigir manutenção especializada, como a substituição de componentes eletrônicos ou a realização de testes avançados. Se você suspeitar que o inversor precisa de manutenção que vai além das habilidades da sua equipe, é hora de chamar um especialista. Esses profissionais têm acesso a ferramentas e equipamentos que podem não estar disponíveis internamente, garantindo que o trabalho seja realizado de forma eficiente e segura.
9. Consultas a Normas de Segurança
Se você não tem certeza se o inversor está em conformidade com as normas de segurança e regulamentações aplicáveis, é aconselhável consultar um profissional. A conformidade com as normas de segurança é fundamental para garantir a operação segura do equipamento e proteger os operadores. Um técnico especializado pode realizar uma avaliação completa e garantir que o inversor esteja em conformidade com todas as exigências legais.
10. Planejamento de Manutenção Regular
Por fim, é sempre uma boa prática planejar manutenções regulares com profissionais especializados. A manutenção preventiva realizada por técnicos qualificados pode ajudar a identificar problemas antes que se tornem falhas graves, prolongando a vida útil do inversor e garantindo seu desempenho ideal. Além disso, esses profissionais podem fornecer orientações sobre as melhores práticas de operação e manutenção, ajudando a otimizar o uso do equipamento.
Em resumo, saber quando chamar um profissional especializado para o conserto de inversores Weg é fundamental para garantir a eficiência e a segurança das operações. Ao observar sinais como falhas intermitentes, códigos de erro complexos, superaquecimento persistente, ruídos anormais e danos visíveis, é importante buscar a ajuda de um técnico qualificado. A experiência e o conhecimento desses profissionais podem fazer toda a diferença na manutenção e no desempenho do equipamento, evitando problemas futuros e custos elevados com reparos.
6. Custos e Tempo de Reparação de Inversores Weg
Quando se trata de reparar inversores Weg, entender os custos e o tempo envolvidos é fundamental para o planejamento financeiro e operacional das empresas. Os custos de reparação podem variar significativamente com base em diversos fatores, incluindo a natureza do problema, a complexidade do conserto e a necessidade de peças de reposição. A seguir, discutiremos os principais aspectos que influenciam os custos e o tempo de reparação de inversores Weg.
1. Diagnóstico Inicial
O primeiro passo para determinar os custos de reparação é o diagnóstico inicial. Muitas vezes, as empresas optam por contratar um profissional especializado para realizar essa avaliação. O custo do diagnóstico pode variar, mas geralmente fica entre R$ 100 e R$ 300, dependendo da complexidade do problema e da localização do serviço. Um diagnóstico preciso é essencial, pois ajuda a identificar a causa raiz do problema e evita gastos desnecessários com reparos inadequados.
2. Tipo de Problema
Os custos de reparação também dependem do tipo de problema que o inversor está enfrentando. Problemas simples, como conexões soltas ou a necessidade de limpeza, podem ser resolvidos rapidamente e a um custo relativamente baixo. No entanto, problemas mais complexos, como falhas na placa de controle ou na fonte de alimentação, podem exigir mais tempo e recursos, resultando em custos mais elevados. Em média, os custos de reparação podem variar de R$ 200 a R$ 1.500, dependendo da gravidade do problema.
3. Peças de Reposição
Outro fator importante a considerar são os custos das peças de reposição. Se o diagnóstico indicar que componentes precisam ser substituídos, isso pode aumentar significativamente o custo total da reparação. O preço das peças de reposição pode variar amplamente, dependendo do tipo e da marca. Por exemplo, capacitores e resistores podem custar entre R$ 10 e R$ 50, enquanto placas de circuito podem custar de R$ 500 a R$ 1.000 ou mais. É importante consultar fornecedores confiáveis para obter cotações precisas.
4. Tempo de Reparação
O tempo necessário para reparar um inversor Weg pode variar de algumas horas a vários dias, dependendo da complexidade do problema e da disponibilidade de peças de reposição. Problemas simples, como a substituição de um componente menor, podem ser resolvidos em poucas horas. No entanto, se o problema for mais complexo e exigir a substituição de várias peças ou um diagnóstico mais aprofundado, o tempo de reparação pode se estender por dias. É importante discutir o tempo estimado de reparação com o técnico responsável para planejar adequadamente a operação.
5. Custo da Mão de Obra
Os custos de mão de obra também devem ser considerados ao calcular o custo total da reparação. O valor cobrado por técnicos especializados pode variar de R$ 50 a R$ 150 por hora, dependendo da experiência e da localização. É importante solicitar um orçamento detalhado que inclua o custo da mão de obra, para que você tenha uma visão clara do investimento necessário para o conserto.
6. Garantias e Manutenção Futuras
Ao considerar os custos de reparação, é importante também avaliar as garantias oferecidas pelos serviços realizados. Alguns técnicos podem oferecer garantias sobre o trabalho realizado, o que pode proporcionar uma camada adicional de segurança para o investimento. Além disso, a implementação de um programa de manutenção preventiva pode ajudar a reduzir os custos de reparação no futuro, evitando problemas antes que eles se tornem graves.
7. Comparação de Custos
Antes de decidir sobre um serviço de reparação, é recomendável comparar os custos e os serviços oferecidos por diferentes profissionais ou empresas. Solicitar orçamentos de várias fontes pode ajudar a garantir que você esteja obtendo o melhor valor pelo serviço. Além disso, verifique as avaliações e referências de outros clientes para garantir que você está escolhendo um prestador de serviços confiável e competente.
8. Impacto na Produção
Por fim, é importante considerar o impacto que a reparação do inversor pode ter na produção. O tempo de inatividade do equipamento pode resultar em perdas financeiras significativas, especialmente em ambientes industriais onde a eficiência é crucial. Portanto, ao planejar a reparação, leve em conta não apenas os custos diretos, mas também o custo potencial de interrupções na produção. Em alguns casos, pode ser mais vantajoso investir em um conserto mais rápido, mesmo que isso signifique um custo um pouco mais elevado.
Em resumo, os custos e o tempo de reparação de inversores Weg podem variar amplamente com base em diversos fatores, incluindo o tipo de problema, a necessidade de peças de reposição e os custos de mão de obra. Realizar um diagnóstico preciso, considerar as peças necessárias e discutir o tempo estimado de reparação com um profissional especializado são passos essenciais para garantir que você esteja preparado para os custos envolvidos. Além disso, a implementação de um programa de manutenção preventiva pode ajudar a reduzir os custos de reparação no futuro, garantindo que seu inversor opere de forma eficiente e confiável.
Em conclusão, a manutenção e o conserto de inversores Weg são essenciais para assegurar a continuidade e a eficiência das operações industriais. Ao estar atento aos sinais de falha, realizar diagnósticos precisos e implementar práticas de manutenção preventiva, é possível evitar problemas maiores e custos desnecessários. Além disso, saber quando chamar um profissional especializado e entender os custos e o tempo envolvidos na reparação são aspectos cruciais para uma gestão eficaz do equipamento. Com as informações e dicas apresentadas neste artigo, você estará melhor preparado para manter seus inversores em perfeito funcionamento, garantindo a segurança e a produtividade de suas operações.
Gostou? compartilhe!