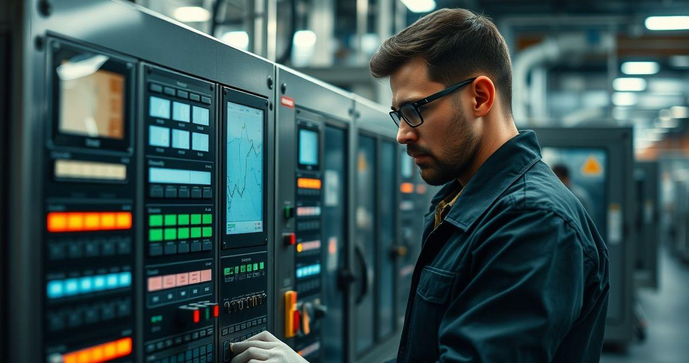
A manutenção em CLP é fundamental para assegurar o bom funcionamento dos sistemas automatizados na indústria. Neste artigo, vamos abordar as melhores práticas e procedimentos que você precisa conhecer para manter seus Controladores Lógicos Programáveis em perfeito estado. Aprenda a identificar problemas, realizar verificações regulares e aplicar soluções eficazes, garantindo eficiência e durabilidade nos processos industriais.
O que é um CLP e sua importância na automação industrial
Um Controlador Lógico Programável (CLP) é um dispositivo eletrônico projetado para realizar operações de controle em sistemas automatizados. Esses dispositivos são amplamente utilizados na indústria para monitorar e controlar processos, máquinas e equipamentos, garantindo eficiência e segurança nas operações.
Os CLPs são programáveis, permitindo que os usuários adaptem seu funcionamento para atender às necessidades específicas de cada aplicação. Isso significa que podem ser reprogramados facilmente para diferentes processos ou alterações na produção, dispensações ou falhas.
A importância dos CLPs na automação industrial é inegável, pois eles melhoram a precisão e a velocidade dos processos, minimizando erros humanos e aumentando a produtividade. Além disso, os sistemas de controle baseados em CLP proporcionam um monitoramento contínuo, possibilitando a detecção antecipada de falhas e melhorando a manutenção preventiva.
Em resumo, os CLPs são a espinha dorsal da automação industrial moderna, facilitando a integração de diversos dispositivos e sistemas, otimizando operações e contribuindo para a competitividade das indústrias no mercado atual.
Tipos de manutenção em CLP: corretiva, preventiva e preditiva
A manutenção em CLP pode ser classificada em três categorias principais: manutenção corretiva, preventiva e preditiva. Compreender essas abordagens é essencial para manter a eficiência e o funcionamento adequado dos Controladores Lógicos Programáveis.
Manutenção Corretiva
A manutenção corretiva ocorre após a identificação de uma falha ou problema no sistema. Essa abordagem é reativa, onde os técnicos respondem a interrupções ou avarias, realizando reparos necessários para restaurar o funcionamento do CLP. Embora crucial, contar exclusivamente com a manutenção corretiva pode resultar em paradas inesperadas e impactos negativos na produtividade.
Manutenção Preventiva
Em contraste, a manutenção preventiva é realizada em intervalos programados, independentemente da ocorrência de falhas. Essa prática visa prevenir problemas antes que eles aconteçam, garantindo que o CLP funcione corretamente e evitando quebras inesperadas. Inspeções regulares, testes de desempenho e substituição de componentes desgastados fazem parte dessa abordagem, que proporciona redução de custos a longo prazo e maior confiabilidade.
Manutenção Preditiva
A manutenção preditiva, por sua vez, utiliza técnicas avançadas de monitoramento e análise de dados para prever possíveis falhas. Sensores e ferramentas de diagnóstico coletam informações sobre o desempenho do CLP, permitindo a identificação de padrões que possam indicar riscos futuros. Essa abordagem possibilita intervenções oportunas, aumentando a vida útil dos equipamentos e otimizando recursos.
Ao entender e aplicar as três modalidades de manutenção em CLP, as indústrias podem garantir que seus sistemas automatizados operem com o máximo de eficiência e segurança, minimizando desperdícios e maximizando a produtividade.
Dicas para realizar a manutenção em CLP corretamente
Realizar a manutenção em CLPs de forma adequada é essencial para garantir a eficiência e a longevidade dos sistemas automatizados. A seguir, apresentamos algumas dicas práticas que podem ajudar na execução correta dessa tarefa.
1. Elabore um plano de manutenção
Crie um plano de manutenção detalhado que inclua atividades programadas, responsabilidades, e prazos. Um calendário de manutenção evita que procedimentos importantes sejam esquecidos e garante que todas as fases da manutenção sejam cobertas.
2. Realize inspeções regulares
Inspecione os CLPs com frequência, verificando conexões, componentes e sinalizações. A identificação precoce de problemas como folgas, corrosão ou aquecimento pode prevenir falhas maiores e interrupções na produção.
3. Atualize o software regularmente
Mantenha o software do CLP atualizado. As atualizações podem incluir melhorias de segurança, correções de bugs e novas funcionalidades que aumentam a eficiência do sistema.
4. Utilize ferramentas adequadas
Utilize ferramentas específicas para a manutenção de CLPs, como multímetros, analisadores de rede e softwares de diagnóstico. Ferramentas apropriadas ajudam a evitar danos ao equipamento durante a manutenção.
5. Capacite a equipe
Garanta que sua equipe esteja bem treinada e capacitada para realizar a manutenção. Conhecimento sobre o funcionamento do CLP e as melhores práticas de manutenção é fundamental para evitar erros e garantir a segurança do processo.
6. Documente tudo
Registre todas as atividades de manutenção, incluindo inspeções, reparos e atualizações. Esses registros são importantes para rastrear o histórico do CLP, identificar padrões e melhorar processos futuros.
Seguindo essas dicas, você pode realizar a manutenção em CLPs de forma eficaz, garantindo que seus sistemas operem com a máxima performance e confiabilidade, diminuindo o risco de falhas e aumentando a produtividade operacional.
Como identificar e solucionar problemas comuns em CLPs
Identificar e solucionar problemas em Controladores Lógicos Programáveis (CLPs) é essencial para garantir a continuidade das operações industriais. Abaixo, apresentamos uma série de problemas comuns que podem ocorrer e como abordá-los de forma eficaz.
1. Falhas de comunicação
Um dos problemas mais comuns em CLPs é a falha de comunicação entre o CLP e outros dispositivos, como sensores e atuadores. Dica: Verifique todas as conexões de cabos e plugues, e confirme se as configurações de comunicação estão corretas. Teste os cabos com ferramentas apropriadas para garantir que não haja danos.
2. Alarmes e mensagens de erro
Os CLPs podem exibir alarmes ou mensagens de erro quando detectam falhas no sistema. Dica: Consulte o manual do usuário para entender o significado das mensagens. Muitas vezes, reiniciar o sistema ou corrigir a configuração ajudará a resolver o problema.
3. Paradas inesperadas
Se o CLP parar inesperadamente, isso pode estar relacionado a superaquecimento, falhas no fornecimento de energia ou problemas de hardware. Dica: Verifique a temperatura do ambiente e o estado do equipamento. Inspecione a fonte de alimentação e certifique-se de que não haja sobrecarga.
4. Ciclos de operação irregulares
Ciclos de operação inconsistentes podem ser causados por erros na programação ou variações nas entradas de sensores. Dica: Analise a lógica de programação para verificar se as condições estão bem definidas e teste cada sensor individualmente para garantir seu funcionamento.
5. Sensores não respondendo
Sensores que não respondem podem afetar o desempenho do CLP. Dica: Realize testes desses sensores para verificar se estão operacionais. Muitas vezes, a substituição de um sensor defeituoso resolve o problema rapidamente.
6. Atualizações de firmware
Às vezes, problemas podem surgir devido a softwares ou firmwares desatualizados. Dica: Verifique a versão do firmware e, se necessário, atualize para a versão mais recente fornecida pelo fabricante.
Ao seguir essas diretrizes, você pode identificar e solucionar problemas comuns que podem surgir em CLPs, garantindo que o sistema funcione corretamente e evitando interrupções na produção. A resolução proativa de problemas é a chave para manter a eficiência operacional na indústria.
Ferramentas essenciais para a manutenção de CLPs
Para garantir uma manutenção eficaz em Controladores Lógicos Programáveis (CLPs), é crucial utilizar as ferramentas adequadas. Abaixo, destacamos algumas das ferramentas essenciais que podem ajudar na realização de diagnósticos, reparos e manutenção preventiva.
1. Multímetro
O multímetro é uma ferramenta fundamental para medir tensão, corrente e resistência. Com ele, é possível verificar se as entradas e saídas do CLP estão funcionando corretamente. Dica: Utilize um multímetro digital, que oferece maior precisão e facilidade de uso.
2. Osciloscópio
O osciloscópio é utilizado para visualizar sinais elétricos em tempo real. Ele permite a análise de formas de onda e pode ser extremamente útil para diagnosticar problemas de comunicação e interrupções. Dica: Familiarize-se com as funcionalidades do osciloscópio, pois seu uso pode ser complexo sem o devido conhecimento.
3. Software de programação e diagnóstico
O software fornecido pelo fabricante do CLP é imprescindível para a programação, atualização e diagnóstico do sistema. Com esse software, é possível realizar testes e acompanhar o desempenho do CLP em tempo real. Dica: Mantenha sempre a versão mais atualizada instalada e faça backups frequentes das programações feitas.
4. Ferramentas de estimativa de segurança
Equipamentos de segurança, como luvas e óculos de proteção, são essenciais ao trabalhar com eletricidade e em ambientes industriais. Dica: Nunca descuide da segurança pessoal durante a manutenção em CLPs, mesmo nas tarefas mais simples.
5. Cabos de teste e adaptadores
Cabos de teste e adaptadores são necessários para realizar conexões temporárias e testar a funcionalidade de diferentes dispositivos conectados ao CLP. Dica: Utilize cabos de qualidade para evitar problemas de sinal e garantir medições precisas.
6. Documentação técnica
A documentação técnica do CLP, incluindo manuais e diagramas, é uma ferramenta essencial para entender o funcionamento do sistema e identificar problemas. Dica: Tenha acesso fácil a esses documentos durante a manutenção, pois eles contêm informações valiosas para resolver problemas rapidamente.
Utilizando essas ferramentas essenciais, você pode realizar a manutenção de CLPs com mais eficácia e segurança, garantindo que os sistemas operem de forma otimizada e minimizando o risco de falhas inesperadas.
Benefícios da manutenção em CLP para a indústria
A manutenção adequada em Controladores Lógicos Programáveis (CLPs) traz uma variedade de benefícios significativos para a indústria, impactando diretamente na eficiência operacional e na sua competitividade. A seguir, destacamos os principais benefícios associados à prática de manutenção em CLPs.
1. Aumento da eficiência operacional
Uma boa manutenção garante que os CLPs e os sistemas automatizados funcionem em níveis ótimos. Isso minimiza as taxas de falhas e melhora a resposta do sistema às demandas de produção, resultando em um aumento geral na eficiência das operações.
2. Redução de custos
A manutenção preventiva e preditiva ajuda a evitar paradas inesperadas e reparos emergenciais, que costumam ser mais caros e impactam na produtividade. Ao realizar manutenções regulares, os custos de operação a longo prazo podem ser significativamente reduzidos.
3. Aumento da vida útil dos equipamentos
Com a manutenção adequada, a vida útil dos CLPs e dos sistemas aos quais estão conectados é prolongada. Tecnologias bem mantidas tendem a operar por mais tempo, permitindo que o investimento inicial seja amortizado ao longo dos anos.
4. Melhoria na segurança operacional
A manutenção regular contribui para a segurança do ambiente de trabalho. Equipamentos em boas condições operacionais são menos propensos a causar acidentes, tornando as operações mais seguras para os operadores e reduzindo riscos de danos materiais.
5. Redução do tempo de inatividade
Com um plano de manutenção bem estruturado, as indústrias podem reduzir o tempo de inatividade causado por falhas inesperadas. Isso se traduz em uma produção mais contínua e previsível, evitando paradas que podem ser prejudiciais ao negócio.
6. Otimização de processos
A manutenção em CLPs permite que os gestores realizem ajustes e melhorias contínuas nos processos de produção. Com informações precisas sobre o funcionamento dos sistemas, é possível identificar áreas para otimização e implementação de melhores práticas.
Em resumo, os benefícios da manutenção em CLPs vão além da simples solução de problemas, gerando impactos positivos na eficiência, segurança e custos operacionais da indústria. Investir em manutenção é, portanto, uma estratégia inteligente que traz retorno significativo a longo prazo.
Conclusão
Após explorar a importância da manutenção em Controladores Lógicos Programáveis (CLPs) e suas várias abordagens, fica evidente que a prática de manutenção traz benefícios essenciais para a indústria. A adoção de métodos corretivos, preventivos e preditivos não apenas garante a eficiência operacional, mas também prolonga a vida útil dos equipamentos e minimiza custos desnecessários.
Além disso, investir na capacitação da equipe, utilização de ferramentas adequadas e acompanhamento rigoroso de procedimentos pode melhorar ainda mais a performance dos CLPs e, consequentemente, as operações industriais como um todo. A segurança do ambiente de trabalho também é reforçada com práticas de manutenção regulares, criando um espaço mais seguro para os colaboradores.
Portanto, não subestime a importância de uma boa manutenção em CLPs. Convidamos você a aplicar as estratégias discutidas aqui em sua operação e observe as melhorias na eficiência e na produtividade. Se surgirem dúvidas ou você desejar compartilhar suas experiências, sinta-se à vontade para entrar em contato conosco. Estamos aqui para ajudar!
E você, como pretende implementar essas práticas de manutenção em sua empresa? Pense em como essas atividades podem transformar sua operação hoje mesmo!
Gostou? compartilhe!